As I’ve mentioned in previous posts over the years, while I’m not the handiest or craftiest guy, I do make an effort to expand my DIY skills when I can. One thing that often leaves me scratching my head is purchasing lumber whenever I take on a project that requires it.
You’d think lumber would be simple; it’s just going and buying a piece of wood, right? But it’s surprisingly complex. There are so many choices that, even with a supply list in hand, I often find myself wandering the lumber section at the home improvement store for 20 minutes trying to figure out which pieces of wood I should buy. Common board? Structural? C or D grade plywood? Pressure treated?
Whenever I’ve done research on lumber, I could find some of the information that I needed in one place, and some of it in another. But I could never find one comprehensive resource that offered all the nitty gritty in a single location. So to consolidate everything for my own purposes, and for our readers, I decided to write this article. I realize most of you won’t be reading through this for enjoyment; what I hope is that you’ll be able to file it away, and refer to it whenever you have a lumber-related question of any kind.
Strap on your tool belt, and let’s do this.
Types of Lumber: Softwood and Hardwood
There are two types of lumber: softwoods and hardwoods. Softwood lumber comes from conifer trees like pine, fir, spruce, and cedar. These woods get their classification for a reason; they can be easily dented with just your fingernail. Softwood lumber also absorbs and loses moisture much easier than hardwoods, so extra care must be taken to maintain the wood’s stability over a lifetime. Pressure treating softwood is one way to maintain its soundness when exposed to the elements. More on that later.
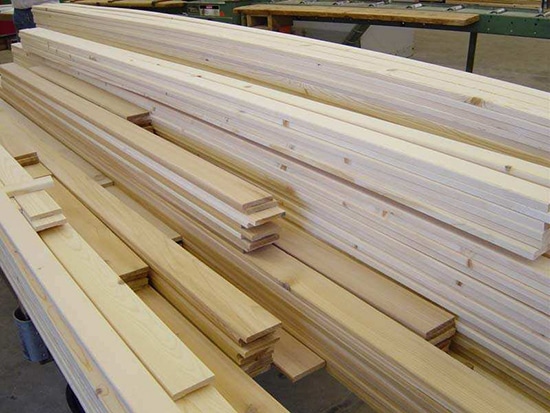
Softwood lumber
Softwood lumber is cheaper because conifer trees grow faster than hardwoods. Consequently, softwood lumber is primarily used in construction, like in framing a house or building a deck. If you’re going to do a home DIY project, you’re likely going to use softwood lumber. You can find it aplenty at your local big box home improvement store.

Hardwood lumber
Hardwood lumber comes from deciduous trees, which have broad leaves that fall off in the cold months. The most common trees you’ll see hardwood lumber come from are oak, maple, walnut, hickory, and mahogany. As you can gather from the name, most hardwoods are harder than softwoods (with the exception of balsa wood), and they aren’t as easily dented.
Hardwood trees take a much longer time to grow to maturity, so the lumber they’re turned into is much more expensive than the softwood variety. Consequently, hardwood lumber is typically used in fine woodworking, furniture construction, cabinetry, and flooring. If you want to get into woodworking, you’ll primarily be using hardwoods. Big box hardware stores don’t stock much of it though, so you’ll often have to visit a specialty woodworking store or a lumberyard to purchase it.
With the basic distinction between softwood and hardwood lumber out of the way, let’s get into the nitty gritty of each type.
Softwood Lumber
Softwood Lumber Classifications and Grades
Because every tree is different, individual pieces of lumber will show a wide range of quality in strength. To ensure that the right kind of lumber is used for the right job, the U.S. Department of Commerce established the American Softwood Lumber Standard.
There are three broad classifications of softwood lumber: Yard, Structural, and Shop and Factory. Let’s take a look at each of them in detail.
Yard Lumber
Lumber intended for ordinary construction and building purposes. Yard lumber is usually graded visually, meaning that an inspector looks at the lumber’s appearance to give it a grade. Yard lumber is broken down into two further categories: common and select.
Common Yard Lumber. Common lumber is suitable for construction and utility purposes, and is graded using a number classification:
- No. 1 Common. Highest quality of common lumber. No. 1 Common lumber will have a few small, tight knots.
- No. 2 Common. Has larger knots than found in No. 1 Common. No. 2 is often used for paneling and shelving and is suitable for general woodworking projects.
- No. 3 Common. Has more and bigger knots than No. 2. The wood is typically damaged and blemished. Well-suited for fences, boxes, and crates.
Select Yard Lumber. Select yard lumber looks much nicer than common lumber because it has no or very few knots. Because of the fine appearance of select yard lumber, it is intended for natural and painted finishes.
Select yard lumber is graded using a letter classification:
- C Select. Almost completely clear of any defects and is widely used in interior trims and cabinets.
- D Select. Has a fine appearance, but contains a few dime-sized knots.
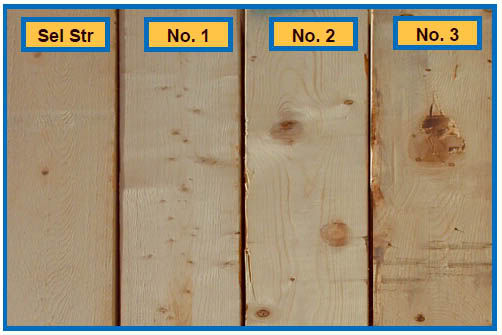
Visual of the various grades. Note how they get uglier and uglier. No. 3 can still be a good piece of wood, it’s just not as pretty as No. 1.
Structural Lumber
If you’ve ever bought a 2×4 or a 4×4, you’ve bought structural lumber. Structural lumber follows a standard dimension for thickness and width. In America the “two-bys” (2x4s, 2x6s, 2x8s, 2x10s) and the 4×4 are the most common structural lumber sizes (though we’ll see in a bit that a 2×4 really isn’t 2 inches thick and 4 inches wide). While the thickness and width is standard, the length is not. You can have a 2×4 that’s six, eight, or even ten feet long. It’s still a 2×4. The standard pre-cut sizes allows carpenters and house framers to buy lumber without having to do as much cutting when they get it to the construction site.
Because structural lumber is heavily used in construction, it’s often machine stress graded so that builders know the bending stress of the board. It can be visually graded, too.
Structural lumber is classified into seven categories:
1. Light Framing. Lumber that’s 2 to 4 inches thick, 4 inches wide. Graded as either Construction, Standard, or Utility. Here’s what those designations mean:
- Construction. Small, tight knots and knotholes permitted with the following guidelines:
Nominal Width | Anywhere on Wide Face | Unsound or Loose Knots & Holes |
2″ | 3/4” | 5/8” |
3″ | 1-1/4” | 3/4” |
4″ | 1-1/2” | 1” |
- Standard. Splits at end of board permitted as long as they’re no longer than the width of the board. Tight knots and knotholes permitted with the following guidelines:
Nominal Width | Anywhere on Wide Face | Unsound or Loose Knots & Holes |
2” | 1” | 3/4” |
3” | 1-1/2” | 1” |
4” | 2” | 1-1/4” |
- Utility. Splits allowed that are equal to 1/6 the width of the piece. Knots are not restricted as to quality and are permitted in the following sizes:
Nominal Width | Anywhere on Wide Face | Unsound or Loose Knot & Holes |
2” | 1-1/4” | 1” |
3” | 2” | 1-1/4” |
4” | 2-1/2” | 1-1/2” |
2. Structural Light Framing. Lumber that’s 2 to 4 inches thick, 2 to 4 inches wide. Graded as Select Structural, 1, 2, or 3. Here’s what those designations mean:
- Select Structural. Pretty much clear of knots. The knots that do exist are small and tight. Strongest of the four grades.
- No. 1. Small, tight knots up to 1-1/2” allowed. Loose knots can only be 1” wide and can only appear once every 3 feet.
- No. 2. Well-spaced knots of any quality up to 2” wide. Can have knotholes that are 1-1/4” wide every 2 feet.
- No. 3. Knots of any quality can be up to 2-1/2” wide. Knotholes allowed every 1-3/4” foot.
3. Studs. Lumber that’s 2 to 4 inches thick, 2 to 4 inches wide. Graded as Stud.
4. Structural Joists and Planks. Lumber that’s 2 to 4 inches thick, 6 inches and wider. Graded as Select Structural, 1, 2, or 3.
5. Beams and Stringers. Lumber that’s 5 inches or thicker with a width more than 2 inches greater than the thickness. Graded as Select Structural, 1, or 2, with Select Structural being the strongest.
6. Posts and Timbers. Lumber that’s 5 inches by 5 inches. Graded as Select Structural, 1, or 2.
7. Appearance Framing. Broad category of structural lumber that’s at least 1 inch thick and 2 inches wide. Aesthetics govern the grading of appearance framing. The highest grades are clear or nearly clear of any knots or blemishes. Appearance framing lumber is used in paneling and siding.There are two primary grades of appearance framing: Finish and Select. Finish grade is higher quality than Select.
Finish grading is only available in lumber from Douglass Firs and Hem-Firs. The grades are Supreme, Choice, and Quality.
Select grading applies to all Western softwood species. The grades are A, B, C, and D:
- A Select. No knots, splits, or other visible defects. Used for fine furniture, exposed cabinetry, trim, and flooring.
- B Select. A few, small defects but nearly perfect. Used for exposed cabinetry, trim, and flooring.
- C Select. Small tight knots. Can be used for shelving and some trim and flooring.
- D Select. Numerous “pin” knots and other small blemishes.
Shop and Factory Lumber
This is lumber that’s selected for “remanufacturing purposes and intended for non-structural applications.” Doors, ladders, pencils, molding, and boxes are typically made from shop and factory lumber. The grading will vary depending on how it’s going to be used. So shop lumber that’s used for doors will have a different grading system than shop lumber used to make pencils. While each use has a different grading nomenclature, the grading is typically based on how much high-quality wood you can get from that piece of lumber for an intended use.
Moisture Content at Time of Manufacturing
In addition to grading the quality of the lumber, lumber grading associations also report the moisture content at the time the wood was turned into lumber (“surfaced”). This is important to know because as a piece of softwood lumber dries, it shrinks. That can change plans for how it’s used on the job site.
- S-GRN. Surfaced in green condition.
- S-Dry. Surfaced dry. Moisture content was less than 19% after manufacture.
- MC15/KD15. Moisture was 15% or less at time of manufacture.
- KDHT. Kiln-dried and heat-treated. Dried to < 19% moisture content with core brought to 56 degrees C for 30 minutes. Heat-treating wood kills insects and fungi spores that can cause decay. Lumber that is shipped globally must be heat treated.
Pulling it All Together: The Lumber Stamp
Next time you’re at the hardware store picking up some wood for your project, look for a stamp on the lumber that looks like this:
STAND & BTR means it’s graded “Standard and Better” light framing. So at a minimum this piece of lumber is standard, but it could be Construction grade, too.
S-DRY means the lumber was surfaced dried.
The Triangle with D-FIR in it lets us know that this piece of lumber came from a Douglas fir.
That little stamp contains all the information that we just talked about above. So with just a glance you can know the type of tree the lumber came from, its classification, its grade, and its moisture content. Pretty cool, huh?
Working With Pressure-Treated Softwood Lumber
Because softwoods are susceptible to rotting from water and fungus, softwood lumber that will be exposed to the elements is often pressure treated with a chemical that preserves the wood. Things like decks, light posts, swing sets, mailbox posts, picnic tables, etc., are often made from pressure-treated lumber.
The pressure treating process is pretty simple. The wood that’s to be treated is stacked into a sealed tank. All the air is vacuumed out, causing the wood’s pores to open. A preservative chemical is pumped into a tank, and pressure is applied to force it deep into the wood’s cells. After the treatment, the wood is removed and left to dry. When you’re at the hardware store, you can tell lumber has been pressure treated by its green hue and slight dampness.
Many of the chemicals used in pressure treating lumber are classified as pesticides by the Environmental Protection Agency, so care should be taken when handling it. Never burn pressure-treated wood in your fireplace or campfire and don’t use it for mulch or compost. And you should consider washing your hands after handling it to get rid of any testosterone-sapping xenoestrogens that may be left on your skin.
Hardwood Lumber
Hardwood Sizes
There aren’t any standard widths for hardwood lumber like there are with structural softwood lumber, but there are standard thicknesses. Hardwood is cut into quarter-inch increments. Below is a chart of the standard thickness of hardwood lumber:
Rough Size | Nominal Size/Name | Actual Dimension (in) | |
---|---|---|---|
(Inches) | (Fraction In) (“quarter”) | S1S1) | S2S2) |
1/2″ | 3/8″ | 5/16″ | |
5/8″ | 1/2″ | 7/16 | |
3/4″ | 5/8″ | 9/16″ | |
1″ | 4/4 | 7/8″ | 13/16″ |
1 1/4″ | 5/4 | 1 1/8″ | 1 1/16″ |
1 1/2″ | 6/4 | 1 3/8″ | 1 5/16″ |
2″ | 8/4 | 1 13/16″ | 1 3/4″ |
3″ | 12/4 | 2 13/16″ | 2 3/4″ |
4″ | 16/4 | 3 13/16″ | 3 3/4″ |
Hardwood Lumber Classification and Grading
Hardwood lumber classification and grading is much simpler than softwood lumber. For hardwoods, appearance is the primary factor in grading. The National Hardwood Lumber Association governs the standard grading system of hardwoods in the United States.
There are four possible hardwood lumber grades. Grade is determined by the amount of clear surface area a particular board has on its poorest looking side (with hardwoods one side will look better than the other). A higher grade board is long and wide with a large percentage of its area defect-free. The clear lumber can be removed from the board with a few large cuts.

Example of a piece of FAS hardwood lumber
- FAS (First and Second). This is the highest quality grade. An FAS board must be at least 6 inches wide, 8 to 16 feet long, and is 83.3% clear on its poorest looking side.
- Select — No. 1 Common. Board that’s at least 3 inches wide, 4 feet long, and is 66.6% clear of blemishes
- Select — No. 2 Common. Board that’s at least 3 inches wide, 4 feet long, and is 50% clear of blemishes.
- Select — No. 3 Common. Board that’s at least 3 inches wide, 4 feet long, and is 33.3% clear of blemishes.
Different hardwoods have different criteria you look for when giving the above grades. You’ll want to check the National Hardwood Association’s website for details.
Common Lumber Defects
Both softwood and hardwood lumber will have defects because of the way the tree it came from grew or from how it was machined during the milling process. While lumber defects can be worked with and incorporated into fine woodworking projects, defects in structural lumber should be kept to a minimum. Be on the lookout for the following common defects:
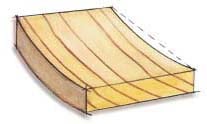
Bow. Warp on the face of a board from end to end.
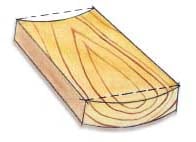
Cup. Hollow across the face of the board.
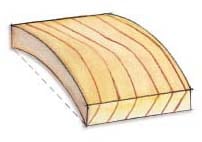
Crook. Warp along the edge line, also known as a crown. This is most common in lumber cut from the center of the tree.
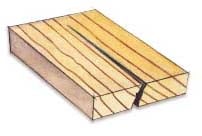
Split. Crack going all the way through the piece of wood, commonly at the ends.
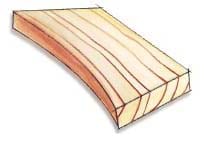
Twist. Warping in lumber where the ends twist in opposite directions.
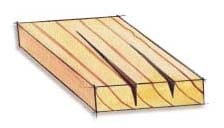
Check. Crack along the wood’s annual growth rings, not passing through the entire thickness of the wood.
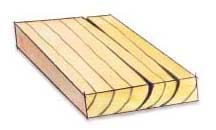
Shake. Separation of grain between the growth rings, often extending along the board’s face and sometimes below its surface.
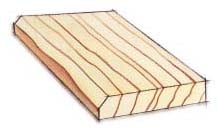
Wane. Missing wood or untrimmed bark along the edge or corner of the piece.
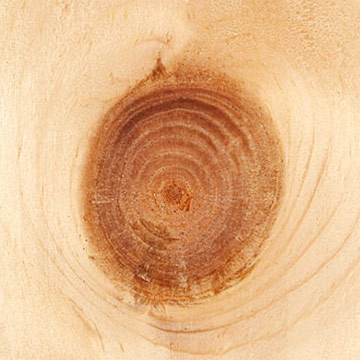
Knots and knotholes. Tight knots are usually not a problem. They’ll stay there. Loose knots may fall out and affect the integrity of the wood.
A 2×4 Isn’t Really a 2×4: Understanding Lumber Sizing
The most common pieces of lumber that you’ll use for projects around the house are “two-bys” and 4x4s. Again, those numbers refer to the thickness and the width of the board. So a 2×4 is a piece of lumber that’s 2 inches thick and 4 inches wide.
Except, not really.
The 2×4 (and the other two-bys) uses what’s called a “nominal” measurement. Mills typically cut a tree into lumber shortly after the tree has been felled, so there’s a lot of moisture in that piece of wood. When the mill cuts a piece of lumber into a 2×4 it actually is 2 inches thick by 4 inches wide. But as the lumber dries during its travel to the lumberyard, it shrinks. By the time you buy that 2×4 it’s actually about 1-1/2” x 3-1/2”, give or take.
So take that into account next time you’re building a project with and buying lumber.
Plywood and Paneling
An article about lumber wouldn’t be complete without discussing plywood. Plywood is heavily used in construction jobs like flooring, roofing, and siding. If you ever decide to make your own plyometrics box for your garage gym (coming soon on AoM!), you’re going to use plywood.
The reason plywood is such a go-to material is that it’s strong, lightweight, and rigid. Due to the way it’s constructed, a single panel of plywood can span great distances without bending. Even if it does crack, it doesn’t crack all the way through.
Plywood is made by layering thin pieces of wood veneer called “plies.” Each layer is alternated 90 degrees from the layer beneath it and then glued together. This layered construction is what gives plywood its strength.
Because only one side of the plywood is seen whenever it’s installed, only one side looks nice and smooth. This side is called the “face.” The rough side is called the “back.”
Plywood can be made from softwood, hardwood, or a combination of the two. Most of the plywood you’re buying from the hardware store for projects around the house is made from softwood lumber.
Plywood Grades
There are a few plywood grading systems out there, but most of them follow an A-D classification with A being the best. Plywood is also classified as Exterior, Exposure 1, Exposure 2, and Interior. The type of plywood you choose will depend on economics, how much exposure to the elements the wood will get, and whether looks are important to you.
- Exterior. Fully waterproof bond (glue) between the layers and designed for applications subject to permanent exposure to weather and moisture.
- Exposure 1. Fully waterproof bond but not for permanent exposure to weather or moisture.
- Exposure 2. Interior type with intermediate bond. Intended for protected construction applications where slight moisture exposure can be expected.
- Interior. Interior applications only.
If you don’t have a lot of money and you don’t care if your plywood is baby smooth on the surface, go for a lower grade. It’s just as strong as the nicer looking grades.
- A. Smooth, paintable surface. Repairs to the veneer like replacing knots with patches can be made, but no more than 18. Used for projects like cabinets.
- B. Solid surface. Minor splitting permitted.
- C. Tight knots and knotholes allowed. Can also have discoloration and sanding defects on the surface as long as it doesn’t impair strength.
- D. Larger knots and knotholes permitted.
You’ll often see plywood with two grades as in “A-C.” This means that the face side is an A grade and the back side is a C grade.
In addition to the above two classifications, plywood is also rated as Sheathing, Stud I-Floor, and siding. This just specifies what a particular end use a piece of plywood was designed for. Most of the plywood you buy from the hardware store for projects around the house like a workbench will be classified as sheathing.
As with softwood lumber, plywood will have a stamp with all this information somewhere on the board. It looks like this:
Well, there you go. Pretty much everything you’ll ever want to know about lumber. Bookmark it so you can come back to it next time you need to go to the lumberyard to buy some wood. I hope you found this useful!
Happy hammering!
______________
Sources
University of Missouri